
Project Recognition.
- Chartered Society of Designers Academic Excellence Award 2018.
- Featured in Oxford Mail.
- Exhibited at New Designers 2018.
The Brief.
Sono was the outcome of a project undertaken in collaboration with Kast Concrete Basins. The brief was to design and create a concrete basin aimed towards a wider more commercial market within the hospitality sector.
The Problem.
The problem was that Kast built products for the home, and wanted to branch out into a wider, more commercial market. Traditional concrete methods limited lead-times and the creation of new products due to the amount of work needed to build one.
By using modern manufacturing methods to rapidly prototype complex moulds and shapes that sped up the process, thus reducing time and labour costs. Especially for Mass Production.
Through the introduction of modern manufacturing processes, the project was able to show the public how versatile ‘liquid stone’ can be which allowed the design to follow a very unique and distinctive shape, whilst providing a fresh product that Kast can add to their existing range.
The product - 'Sono' had its very successful public launch in may of 2018 and has gone to be an incredibly popular product within Kast's range.
Due to my unparalleled and outstanding efforts in the production of the Sono basin, my work was featured and recognised in the Oxford mail.
"A STUDENT working with concrete for the first time is celebrating after his basin design was launched on the open market."
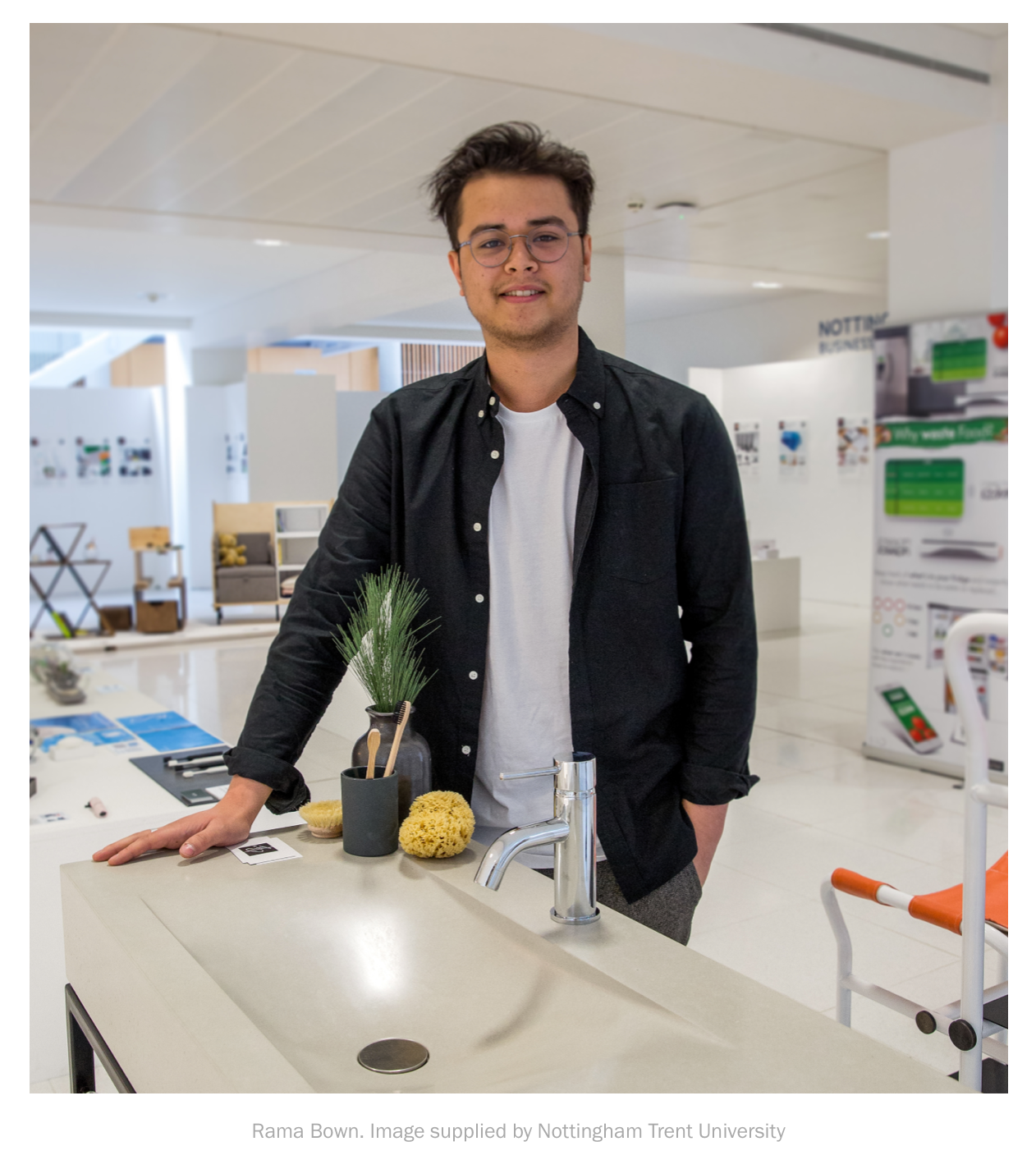
It had also ultimately resulted in me receiving the Chartered Society of Designers Academic Excellence Award in 2018.
I was able to influence the company by producing a concrete product for mass production. I used computer-aided design software to create a 3D model of the basin and was then able to use a computer numerical control machine at the University which allowed me to produce the basin’s distinctive shape in a fibreboard mould.
Having access to a computerised machine made the complex design possible and the process quicker and more cost effective which was a very non conventional way of approaching the manufacture of a basin within the company.

Ideation.
I had developed a range of different designs that explore form and shape and the extent in which concrete can be moulded into. Through extensive development meetings and study groups with Kast, we had narrowed down my designs to ones that would be best suited for the company.
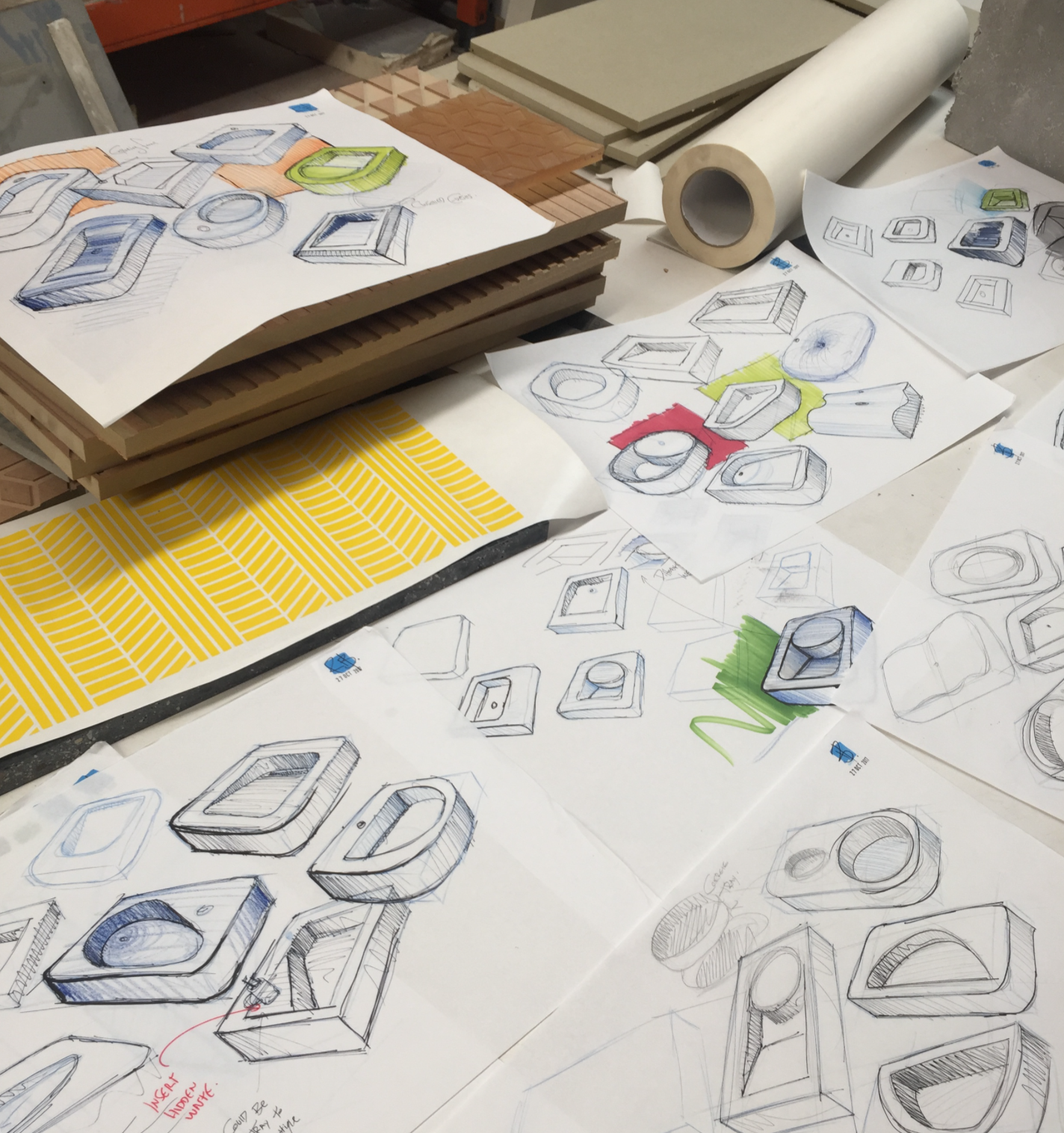
I had learnt to stay within the parameters of the ethos of the company but explore the shape a bit more. The updated Criteria for design became :
Easily Cleanable
To focus on the material
Fixed Waste/no overflows
Scoop within the basin
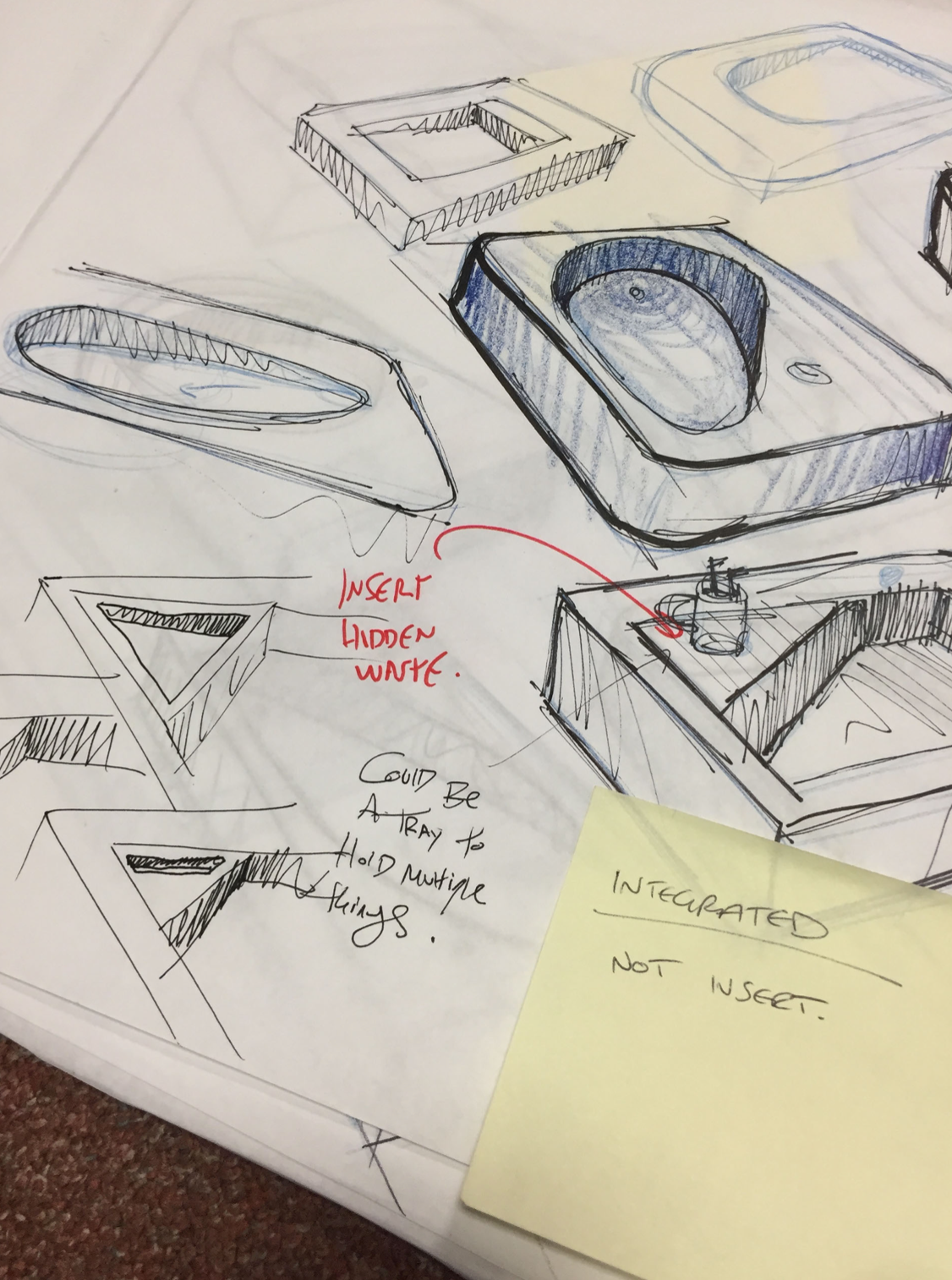

Photos taken from design meeting with the team.
Model Making.
The product mockups from the meetings started off very organic and became simplified, with these ideas in mind I created some quick prototypes from paper and blue foam so give more of an idea to some of the fluid shapes we could potentially create.



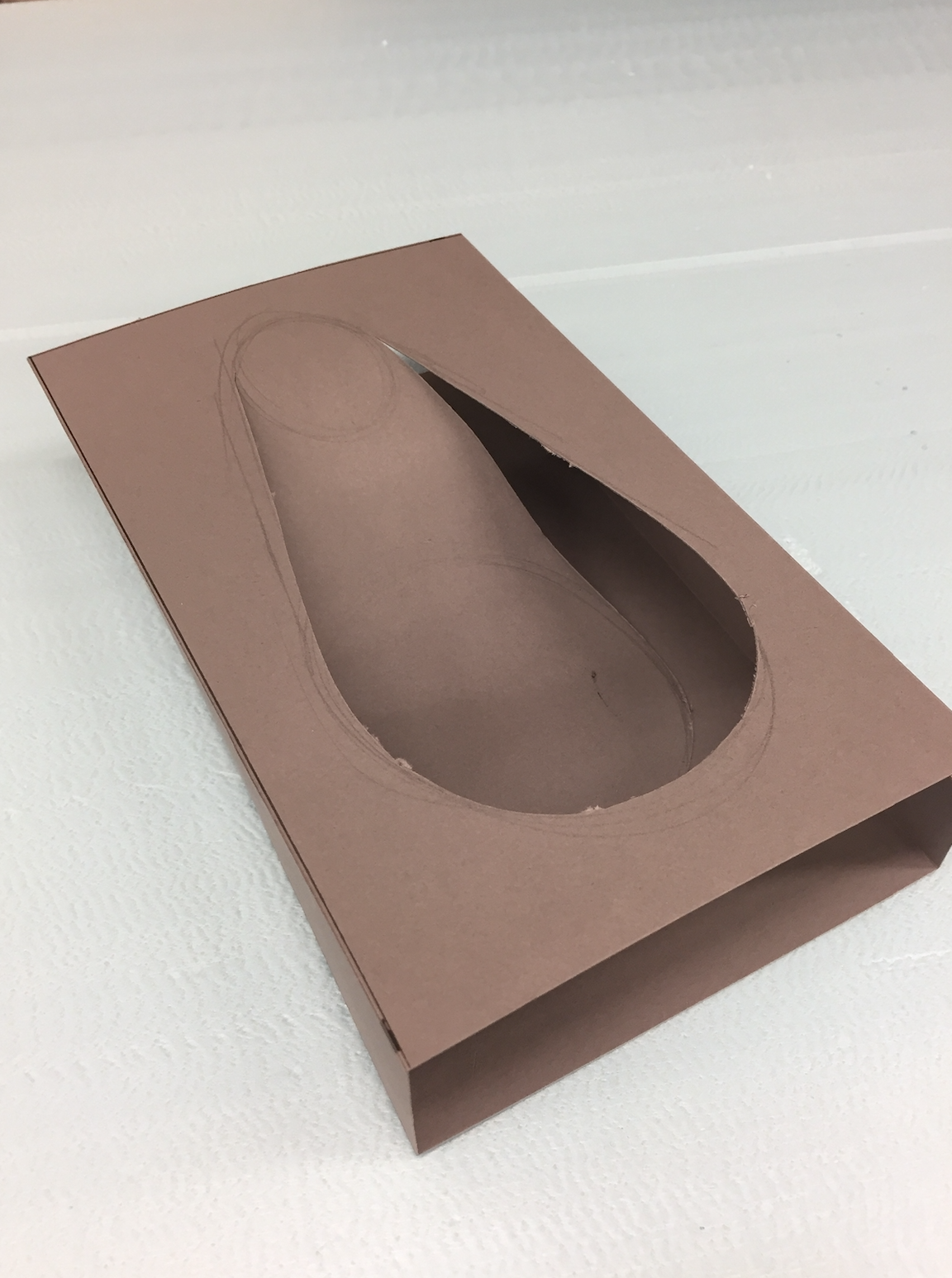
CAD.
With these ideas in mind i took to CAD to develop true renders for the sketches and models that had been taken forward. 3D software proved to be crucial in the ideation stage of the design process.
And through research meetings and revisions to designs, the outcome was a combination of both sharp shaped form and organic flow. Which is something that was not previously financially possible with the labour at hand within the company, this shape was determined possible through the use of Computer Aided Design and resources within my university.



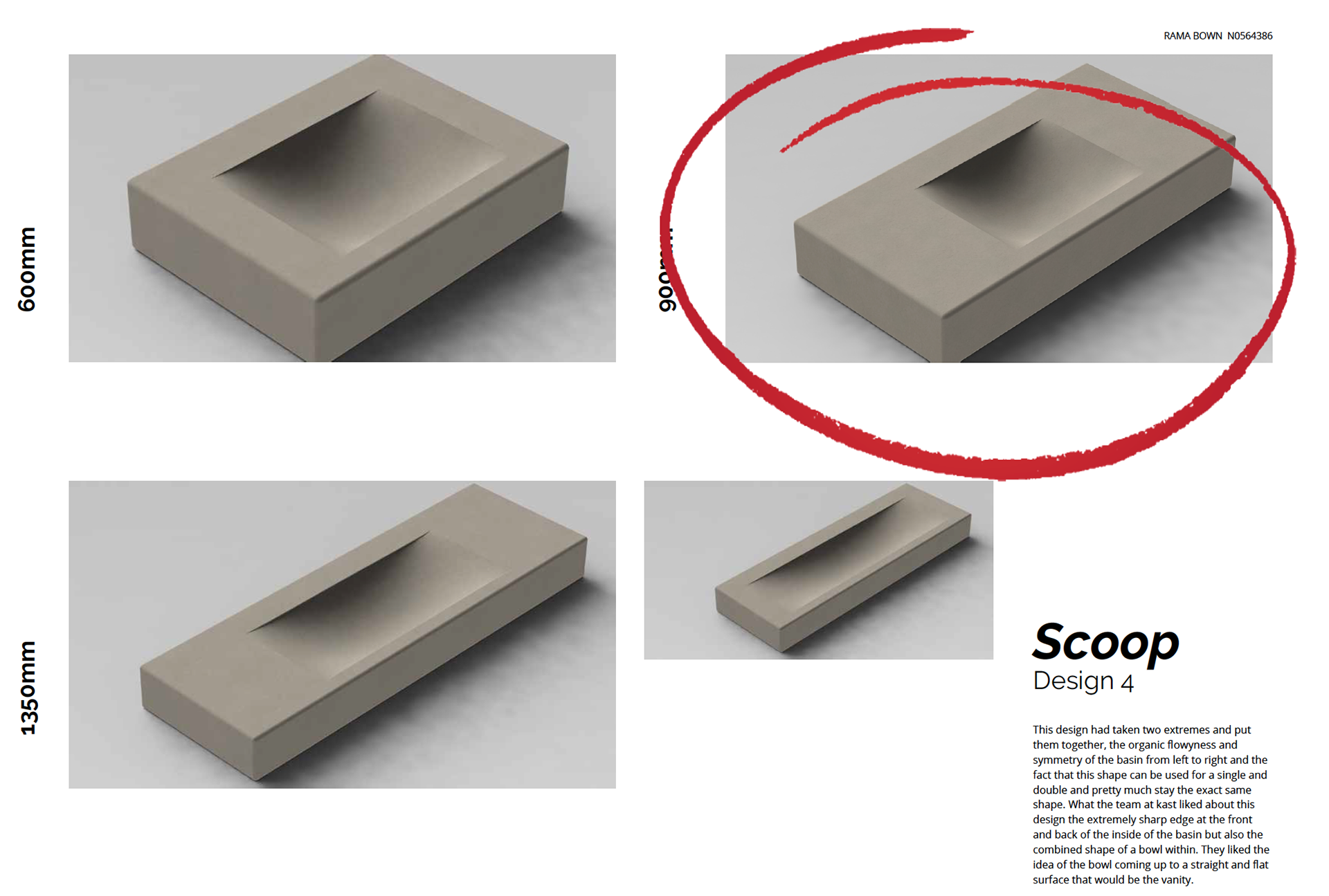
Final Outcome.
The final design was narrowed down to a stylistic and dynamic shape that conformed to legislative laws within the hospitality sector and was designed with vanity space for toiletries in mind. A shape like this that would have previously taken 4 times longer to manufacture by hand but when produced using CNC through initial stages, reduced the labour costs by a factor of 4 as well as speeding up the manufacturing process.
The project was also an experimental one, with the thought of how far an industrial material such as concrete can be pushed to be brought into hospitality and essentially be more commonly used as a great material within the home.
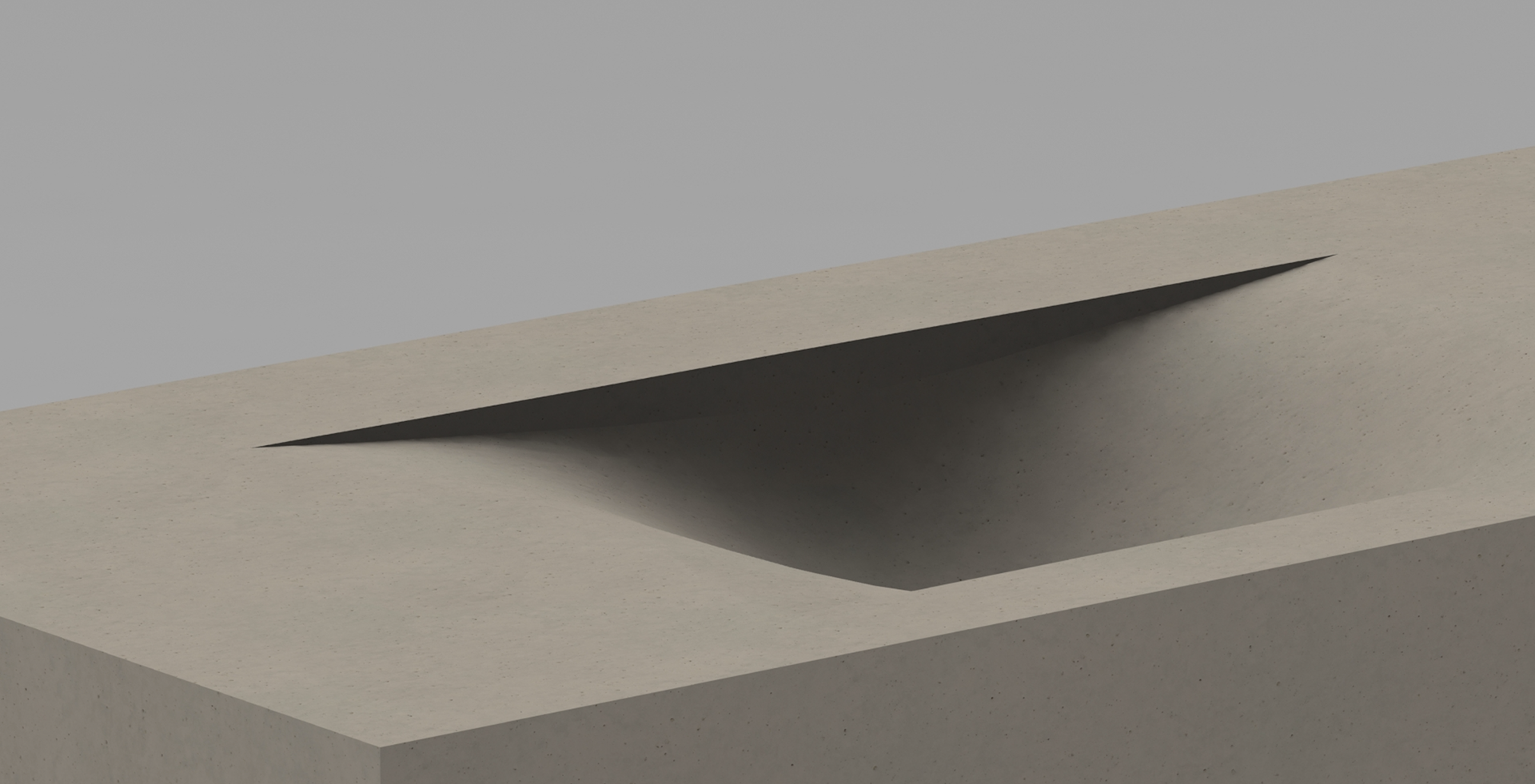
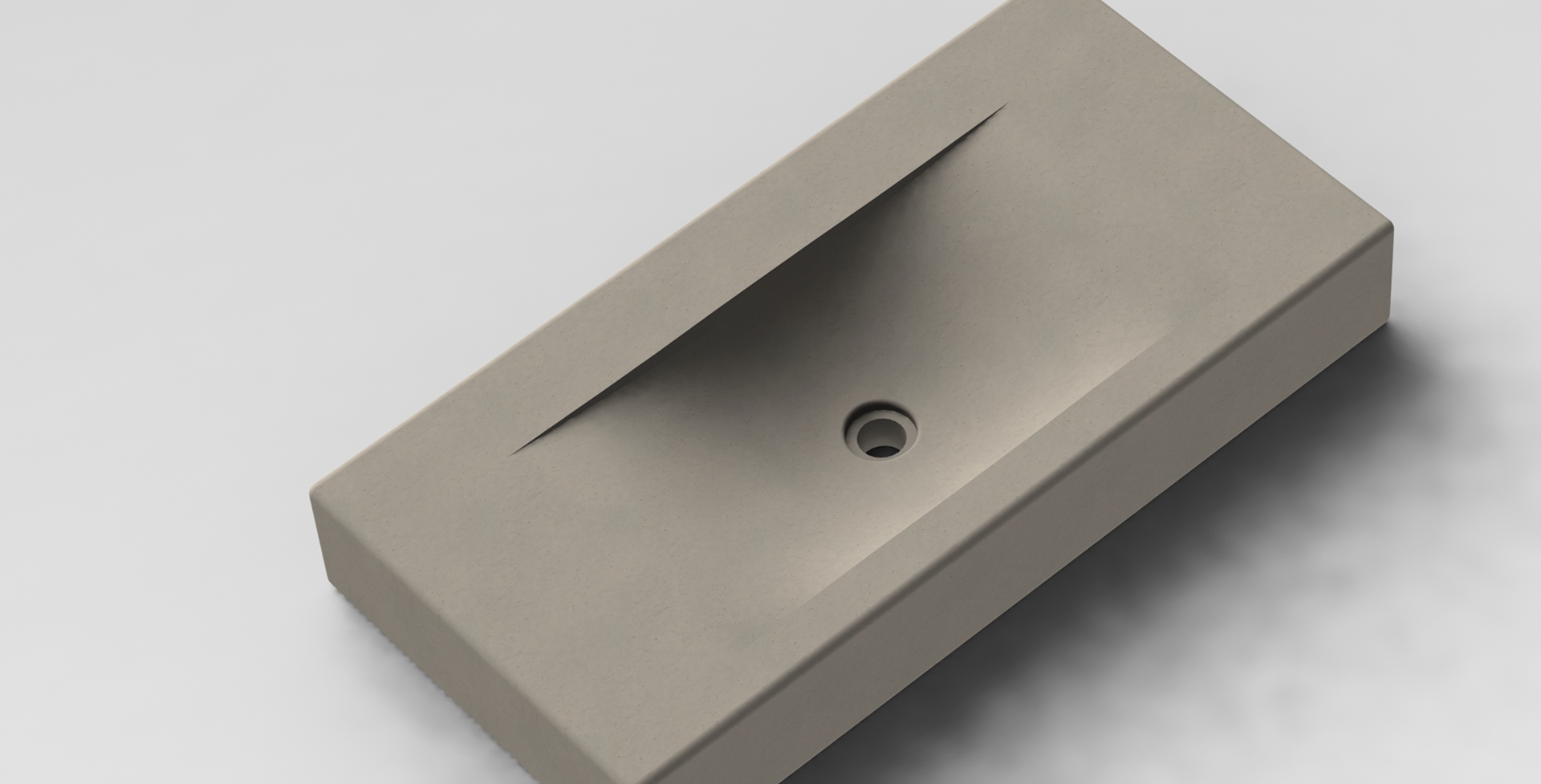
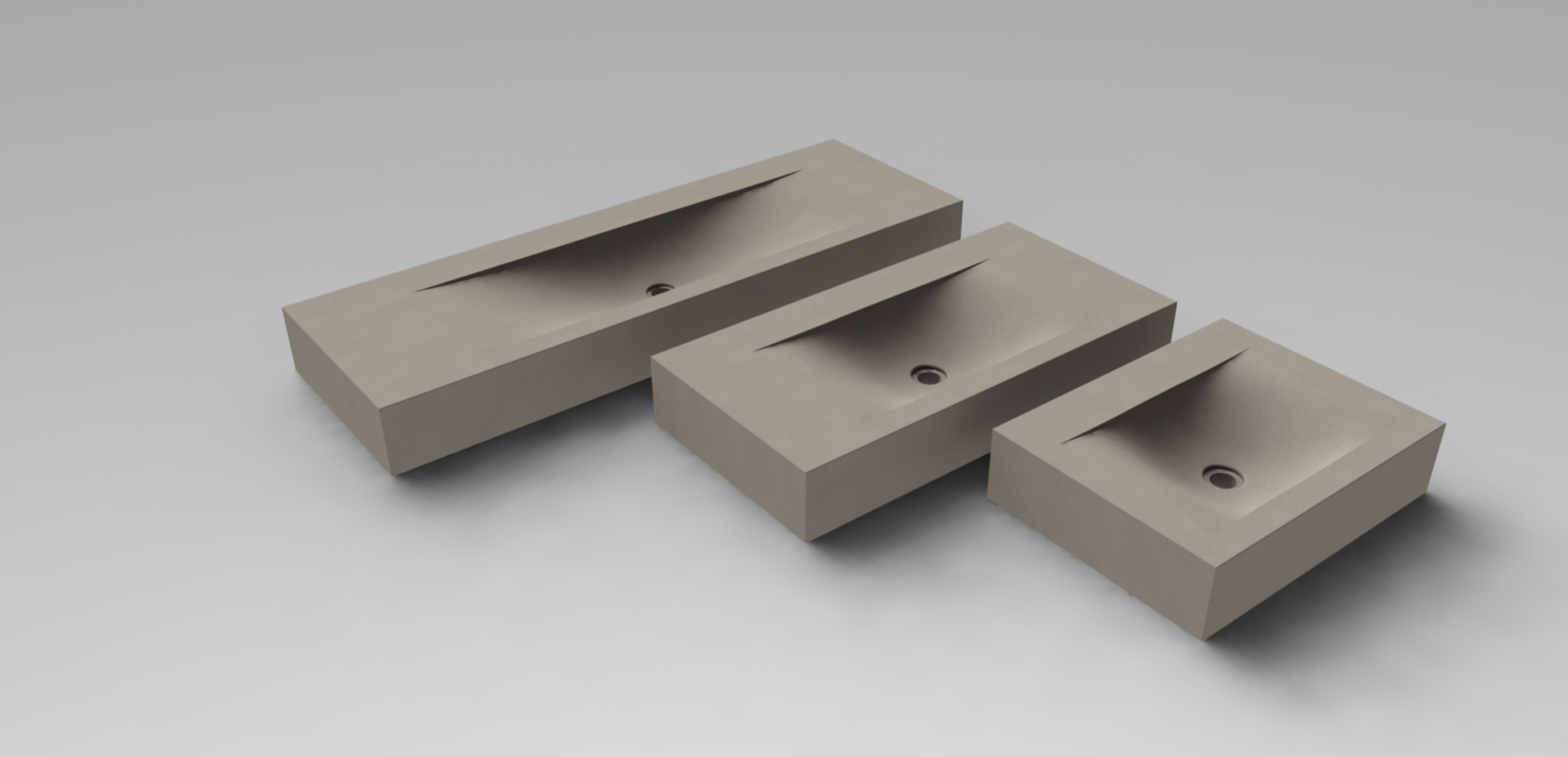
Manufacturing.
The manufacturing of the Sono came round immediately after deciding which design was best suited to fit the brief. With initial lead times of roughly 4 weeks to produce a brand new product within the company, through the use of CAD for beginning stages of the production, it was reduced down to a matter of hours. The whole process entailing creating a mould for the basin to be recast from as this products intent is to be mass produced.
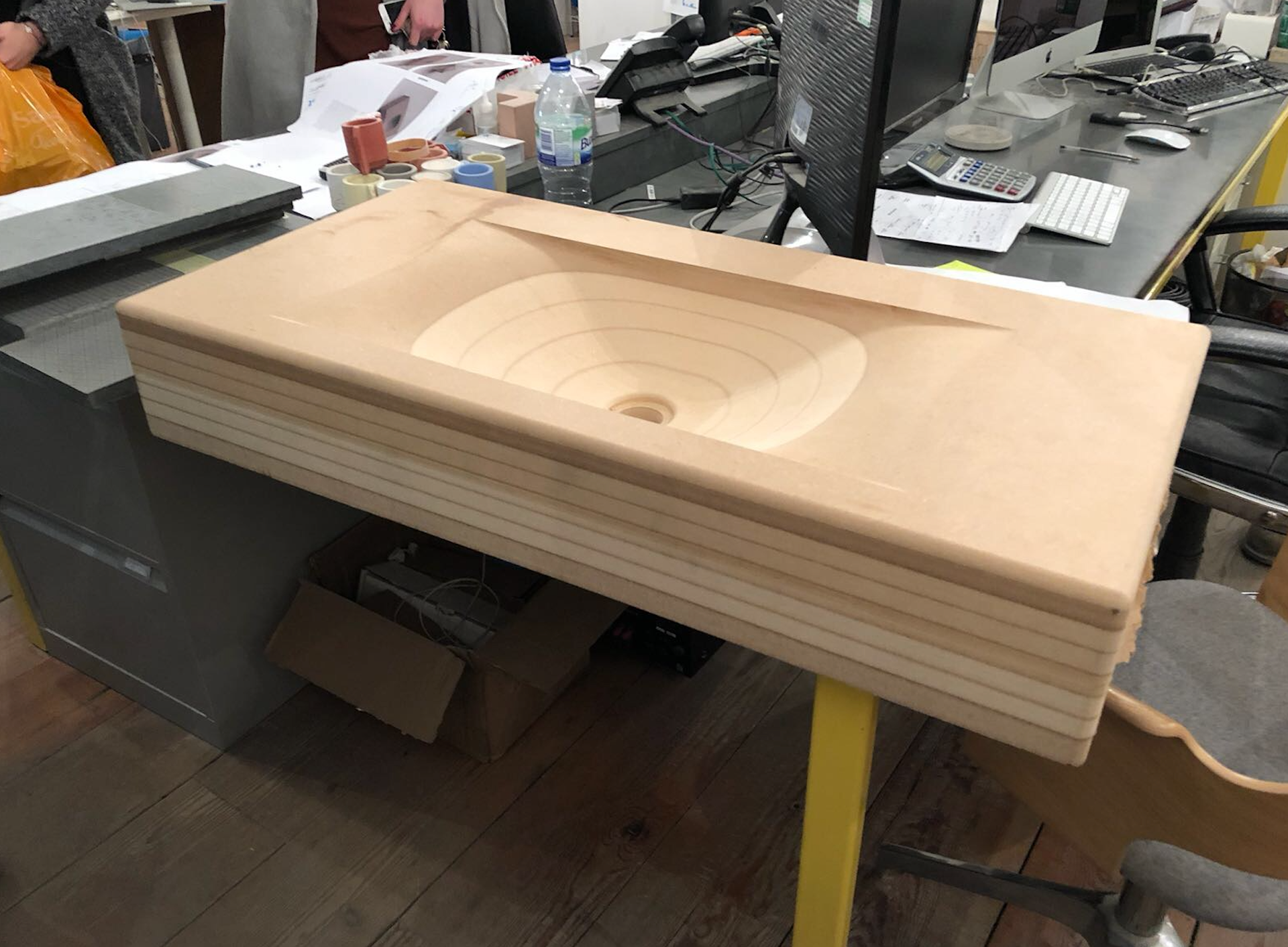
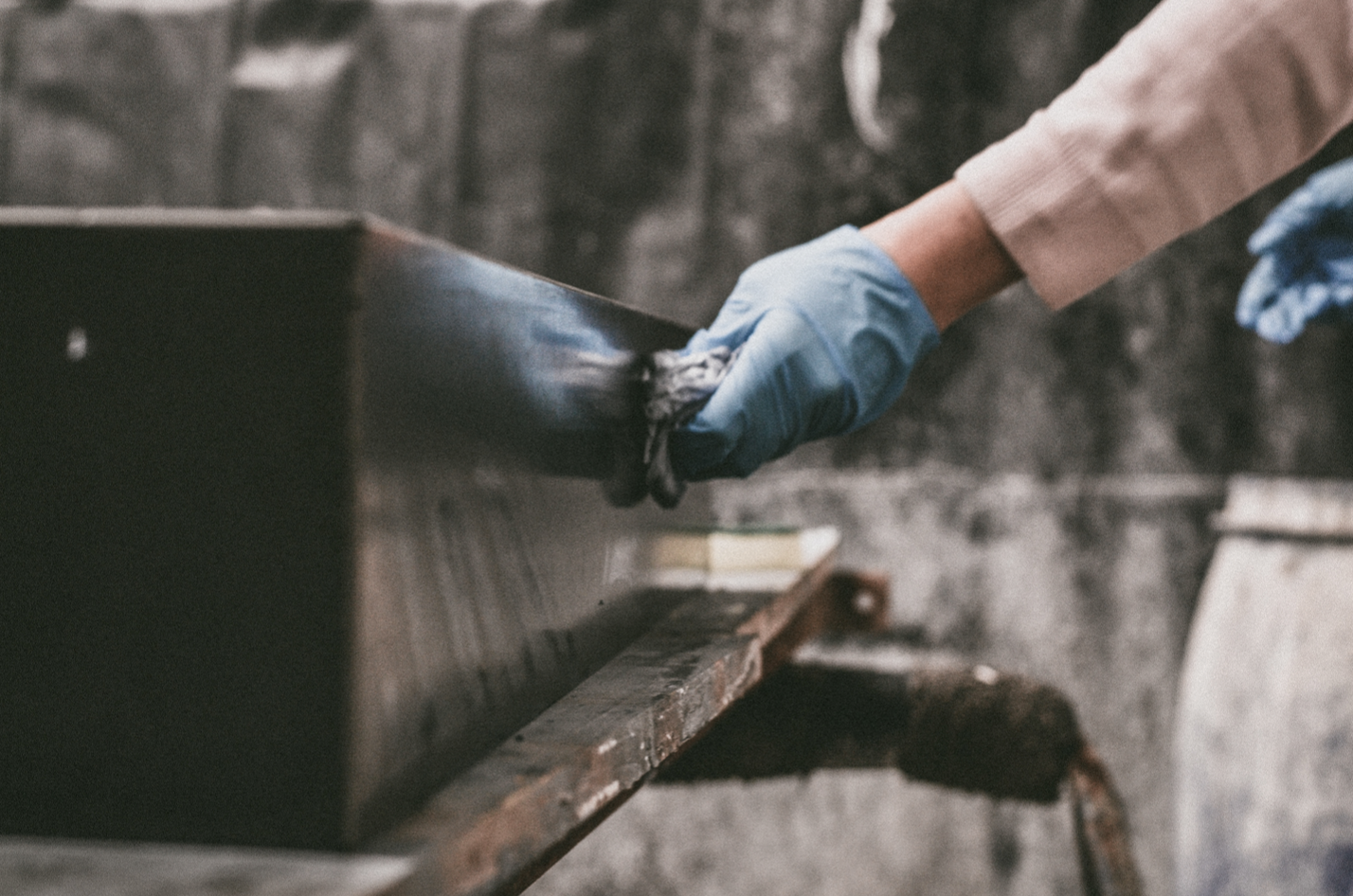
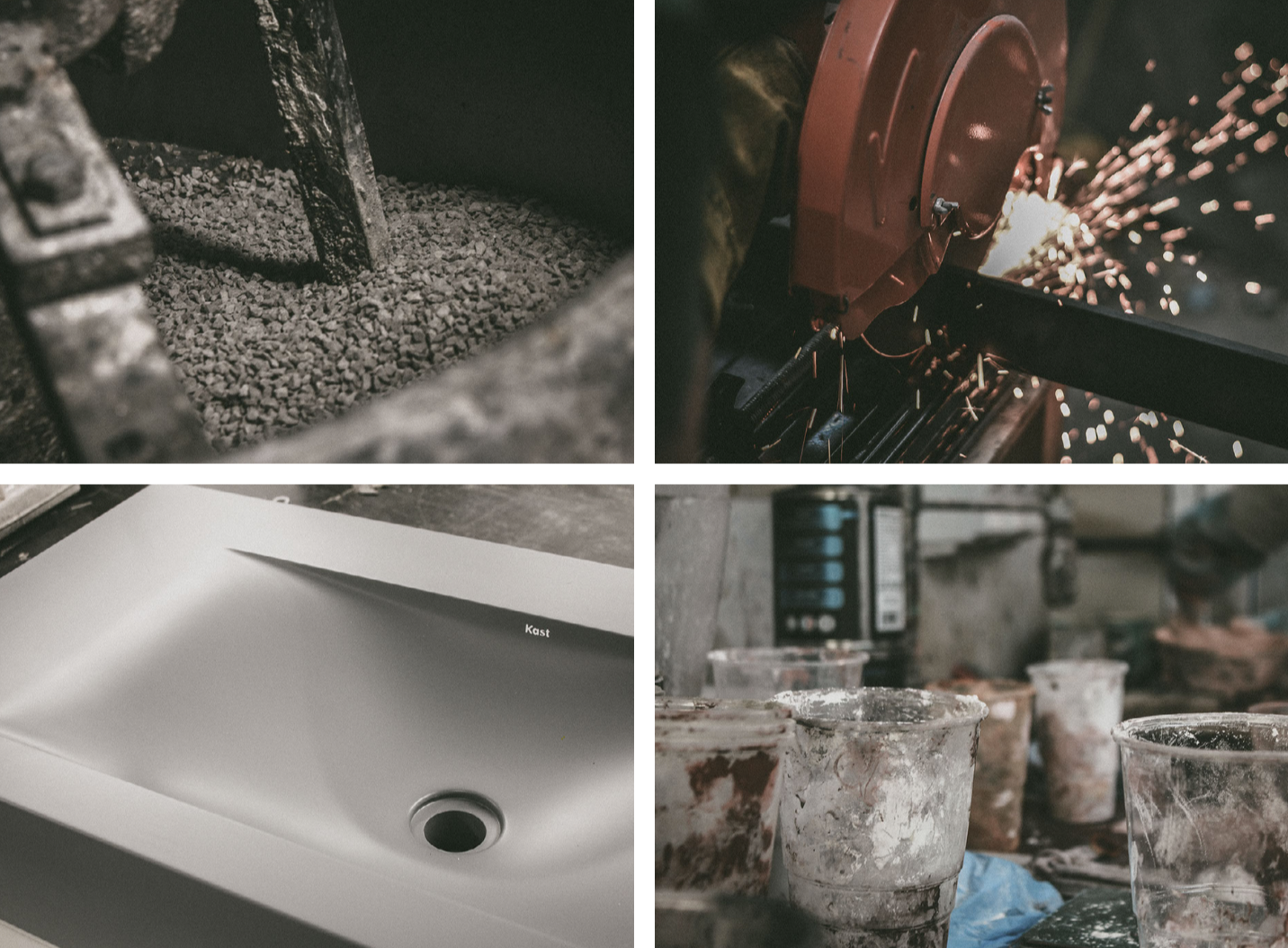
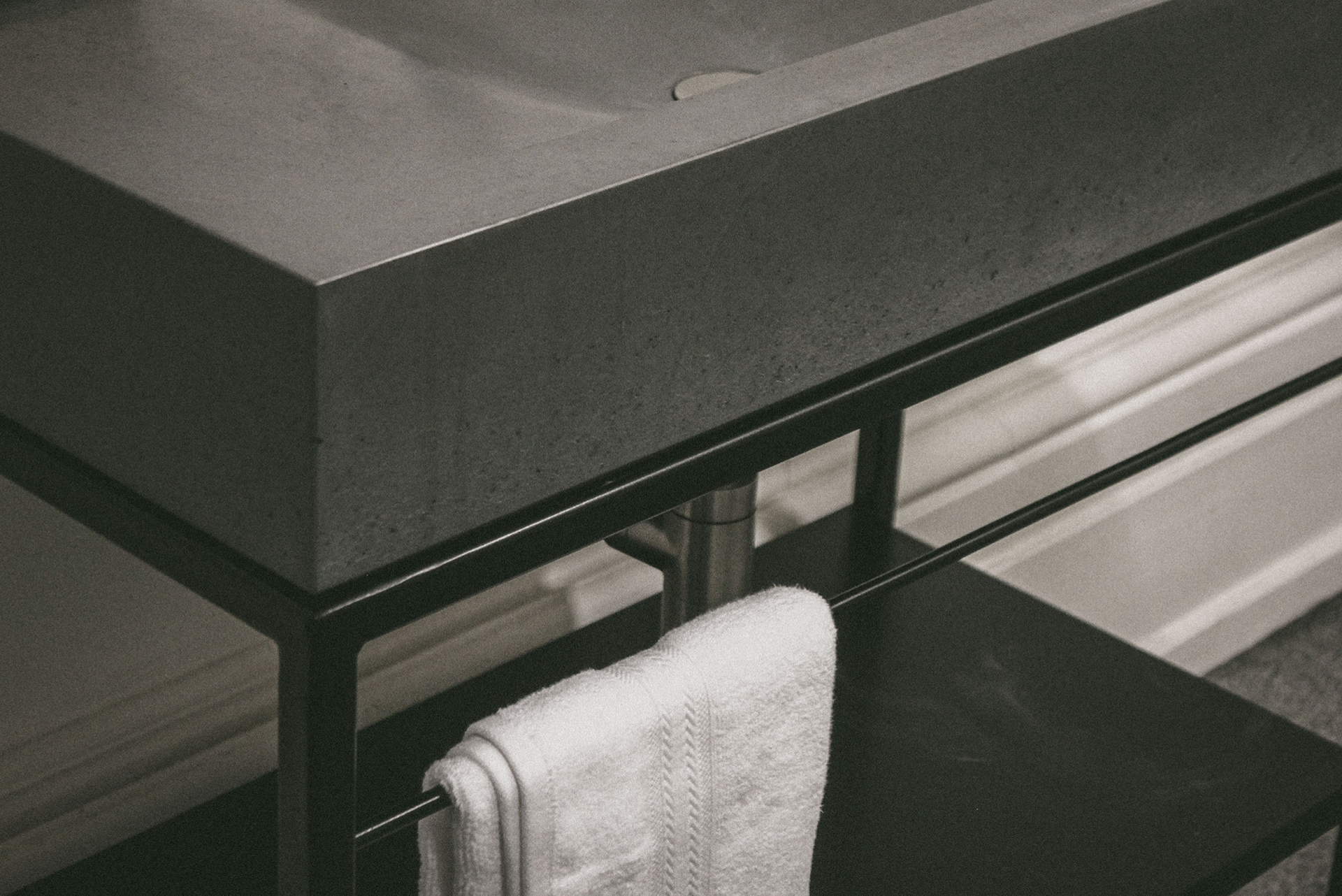
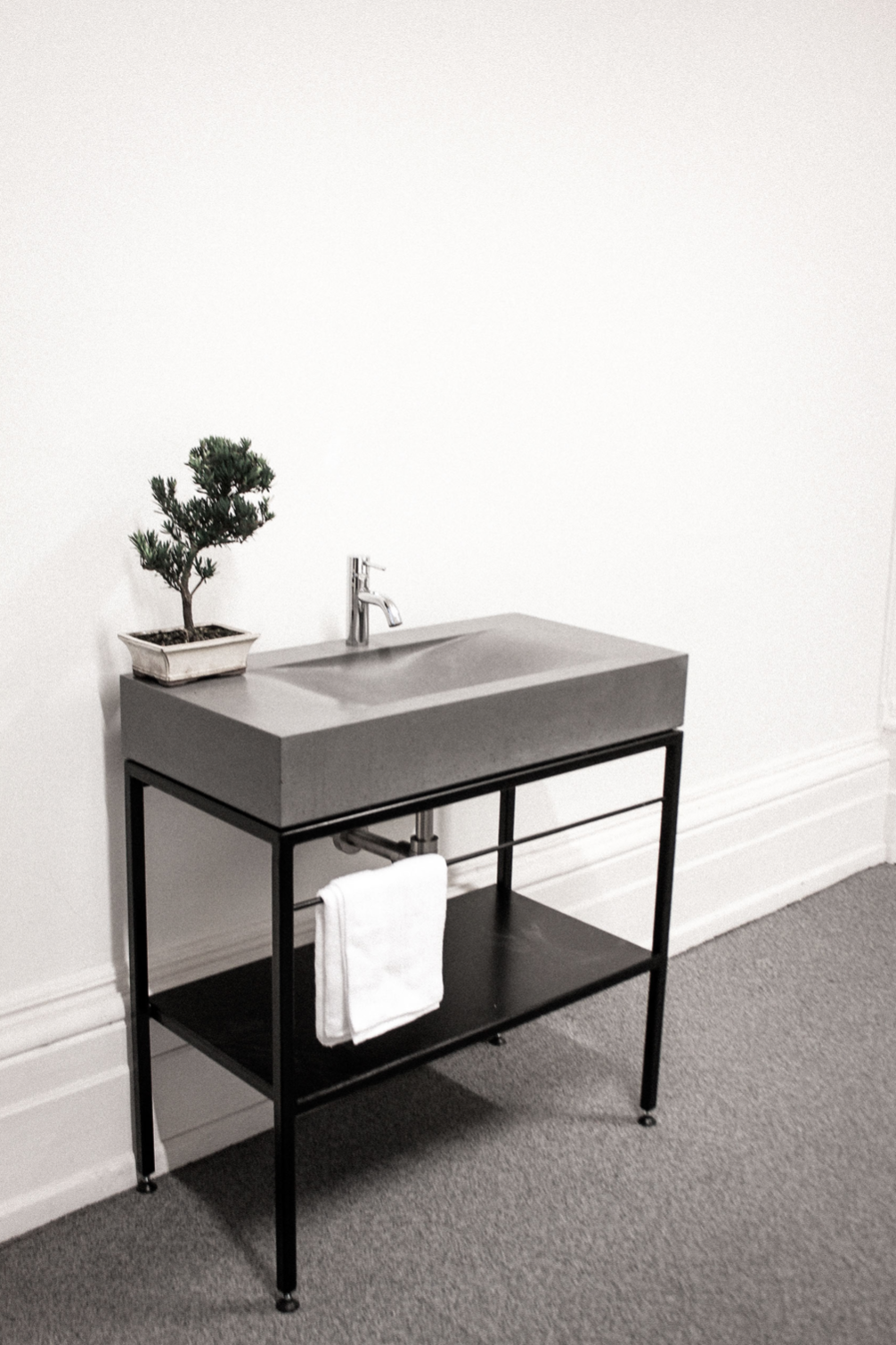
An addition to the basin i had developed and designed a stainless steel powder coated frame that the basin sits on, this was for aesthetic purposes that a heavy concrete product can still look flattering within someones home as a stand alone unit within a hotel room.